Meeting modern construction needs: SIPS vs new panelised solutions
Structural insulated panels (SIPs) have been one of the most popular materials used in modern methods of construction for external walls and roofs, with main contractors choosing them for a variety of commercial buildings including schools, care homes and healthcare and leisure facilities.
However, as the industry accelerates towards new improved compliance and sustainability, contractors’ needs are changing, and SIPs are becoming less suitable to get the job done. However, their previous popularity means that change might well be difficult, as SIPs have become a “catch all” term for a variety of different performing panels. Much like we call vacuum cleaners ‘Hoovers’ and sticky tape ‘Sellotape’, the clarity around what is a SIP, compared to similar panelised solutions, may create confusion especially over performance in relation to compliance and sustainability.
But we’re here to help. To ensure all contractors can continue to create buildings that comply and reflect the needs of their clients as well as the future changes within the industry around building safety, understanding the difference between SIPs and alternative panel options should be a priority.
What are SIPs?
SIPs are a panelised build system for the external structure, and combined with other non-SIP panels, are used for internal walls and floors, and act as an alternative to labour intensive traditional build methods. SIP panels consist of a ridged insulating foam core sandwiched between two structural facings, typically oriented strand board (OSB), which can be used for walls and roofs in MMC buildings.
SIPs can be made with a number of materials. The foam core represents the greatest challenge in regard to building safety. These can consist of either polyurethane (PUR), polyisocyanurate (PIR), or a polystyrene (EPS or XPS), which are all classified as combustible or flammable. Currently, using a non-combustible insulation in a SIP is not possible.
This is where we are different. The materials used in our products contain only non-combustible insulations and boards, offering a clear alternative from the definition above.
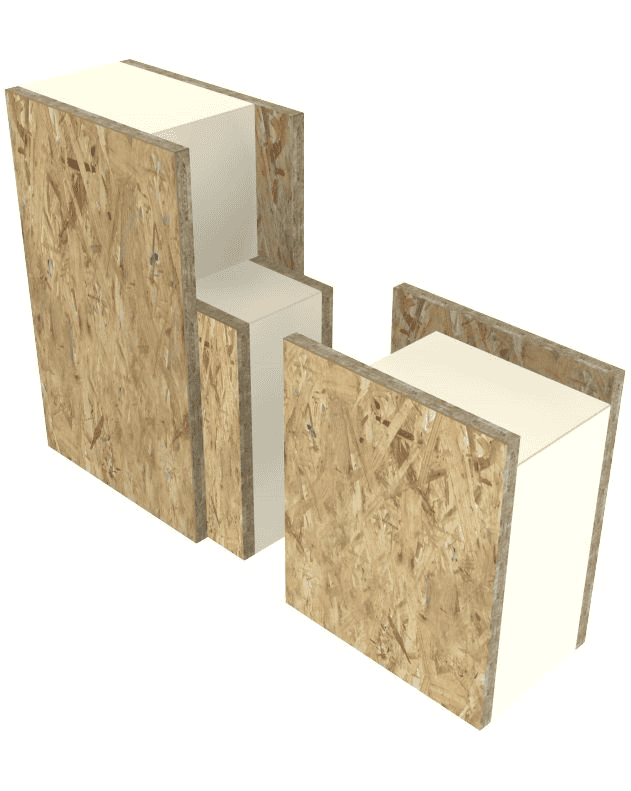
Image: SIP digital model
Why have SIPs been so popular?
Since they are manufactured under factory-controlled conditions, SIPs can be fabricated to accurately fit nearly any building design. Their thin foam core additionally performs well as a thermal insulator, offering maximum energy efficiency.
However, in the face of new compliance and sustainability standards, they are no longer the most suitable panels for contractors to use, particularly in light of new safety regulations, the Building Safety Act, and new safety concerns which have raised a major industry-wide rethink of what is needed to prove compliance in regards to more robust testing.
Dangers of combustibility
Following high-profile incidents, such as the major fire of Grenfell Tower in London in 2017, amendments have been made to the Building Safety Act and Joint Code of Practice – leading to a greater demand for more robust testing and re-prioritisation of compliance in the sector.
This in turn has led many contractors to move away from SIPs, as despite their other benefits, these panels have a number of challenges to overcome, such as the combustible materials used within the foams and boards and the new robust testing required to meet compliance.
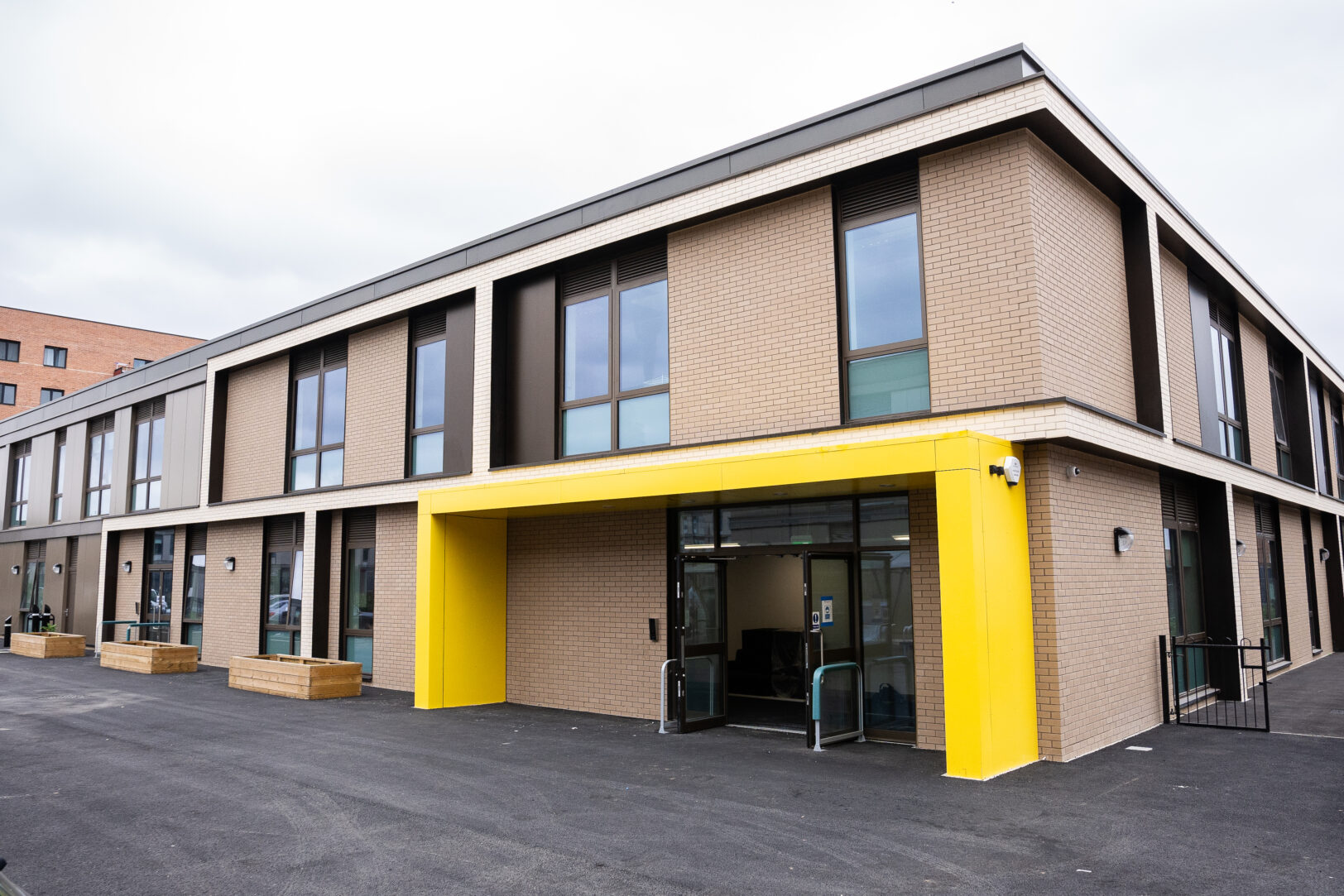
Image: Greatfields School by Net Zero Panels
So, what are the alternatives?
At Net Zero Panels, we’re leading the charge for fire-resistant buildings, through our use of innovative technology, materials and testing of all structural elements. Our solutions combine cost, combustibility, carbon and compliance to design, engineer and produce panels that reflect industry need for safe alternatives to SIPs that are viable, and we must look at the entire structural solution of the building and not just the panel.
Our X-Guard panels exceed industry safety standards with advanced fire-resistant materials, testing and structural design. With our panels, we provide our clients, design teams and main contractors with peace of mind that their building is robust, tested and compliant. The improved efficiency and reduction of embodied carbon also simultaneously supports their journey to net zero.
[Image suggestion: image of different types of panels from NZP]
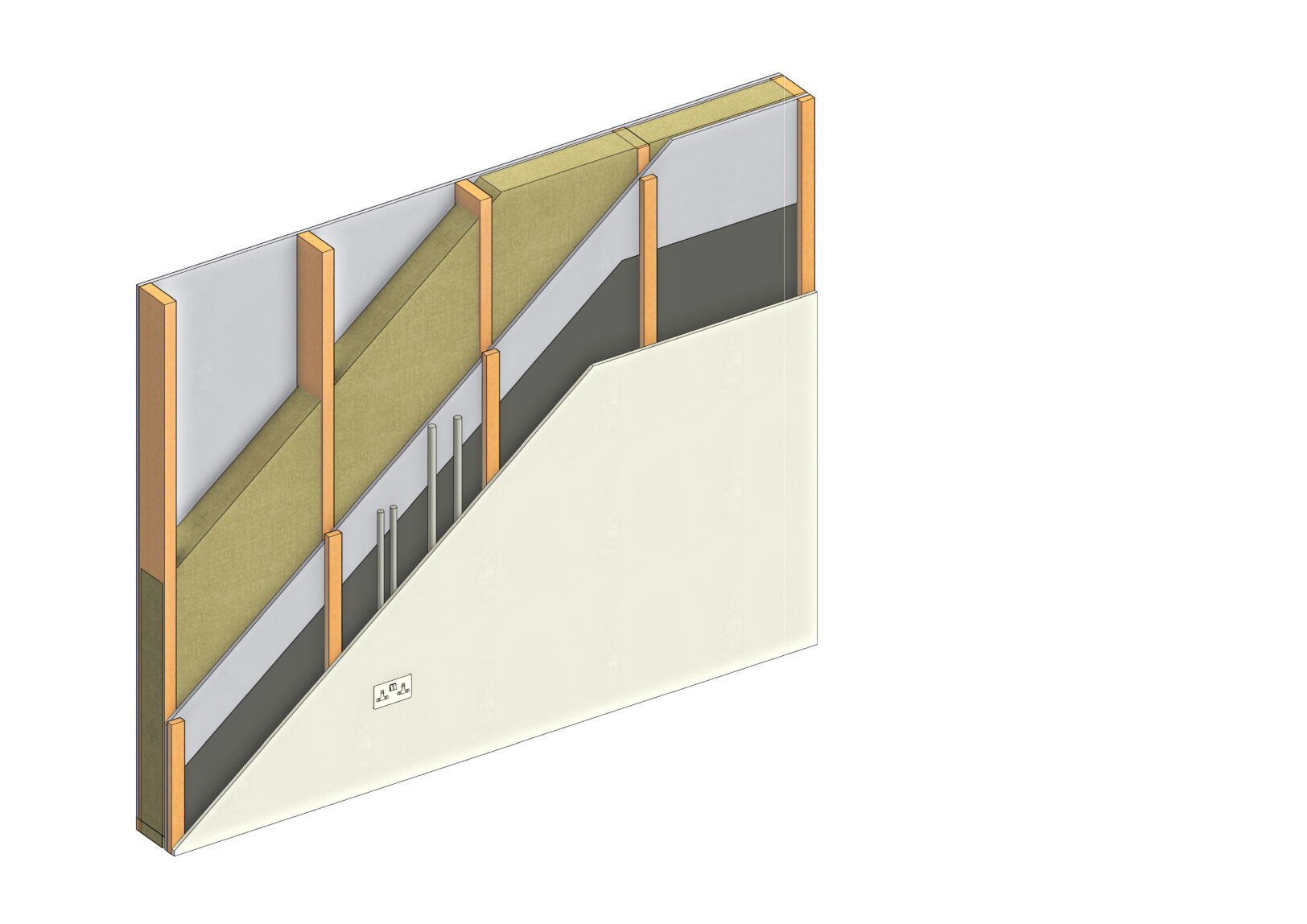
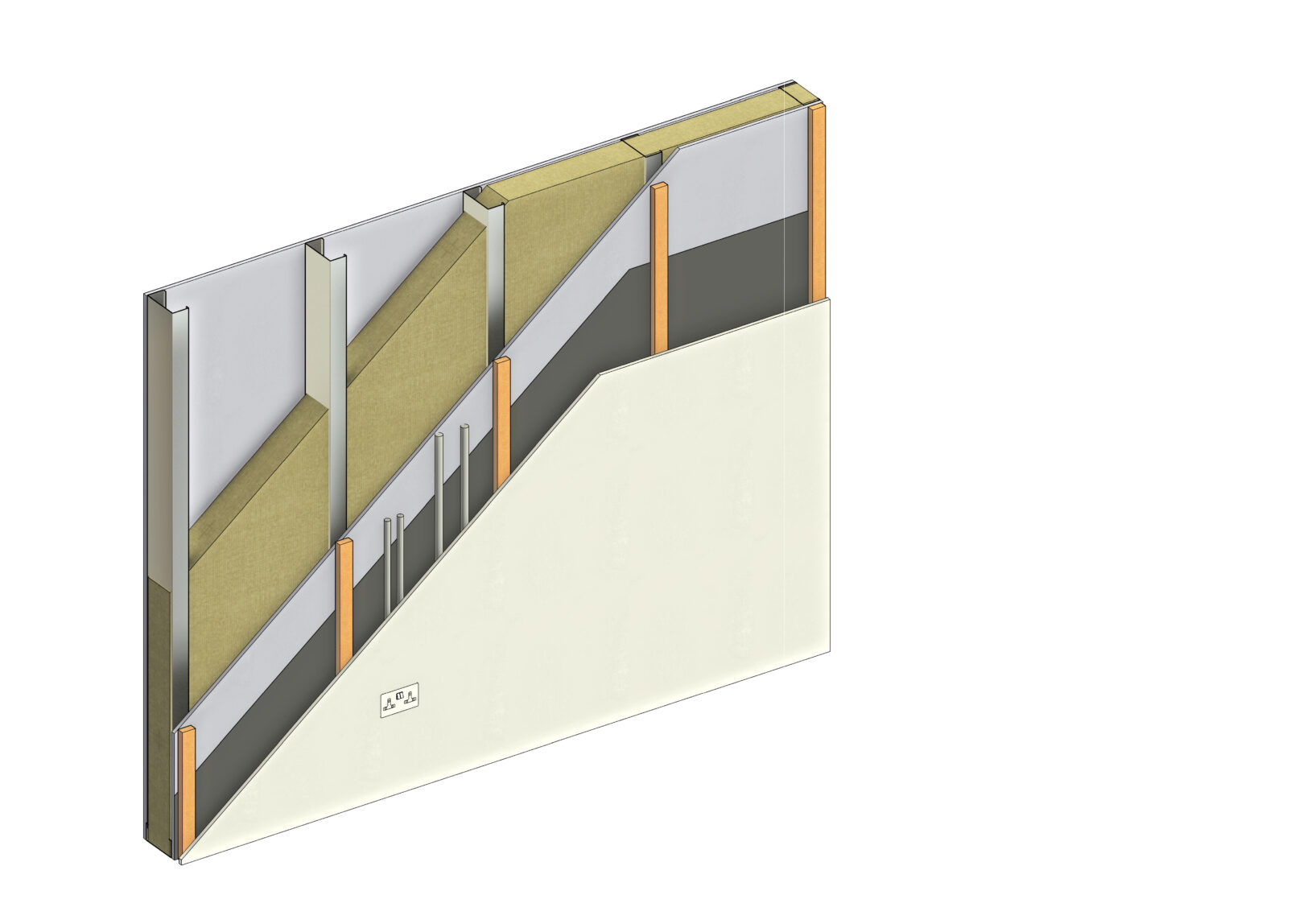
Image: 3D section model of a NZP timber & Steel wall build up.
Reducing risks with flexible solutions
Providing panelised solutions that reflect the needs of the industry whilst focusing on combustibility, attainable costs and reducing whole life carbon is our priority.
Our panels not only improve compliance and sustainability, but the precision manufacture means quick, accurate installation across any project.
The industry is evolving and so is the perfect solution, so it’s time to choose materials that reflect your clients’ needs.
Get in touch to find out more from our compliance experts today